4 Pump Problems and How to Prevent Them
Although there are thousands of factors that determine how long an industrial pump will last, a pump is a costly investment that should make business sense. However, pumps work under varying pressure levels, temperature, and other variables which can take a toll on them.
It is essential to have a professional technician regularly check your pumping system and perform preventative maintenance before any potential system problems get out of hand. Proper troubleshooting can help identify common hitches and restore the pump to optimal capacity.
Below are common problems that affect industrial pump systems.
1. System Leakages
Leaks in your piping system can negatively affect your pump’s performance. Progressive loosening, wear and tear on mechanical joints, vibrations, and expansions caused by hot air in the system are the leading causes of leaks in pumps. A pump engineer can easily repair pipe leaks by replacing corroded seals or tightening loose joints.
Other than the pipes, pump valves are also susceptible to leaks. A qualified technician will tell you when you need to repair or replace your valves. It is paramount that you only work with an expert when handling valve repairs because excessively tight valves can be hazardous.
2. Pumpage Problems
Pumpage is the liquid flowing through a pump system. Environmental and process factors such as temperature fluctuations can change the liquid’s viscosity, and this may, in turn, affect the pump’s flow and efficiency. Problems resulting from pumpage are sometimes only noticeable when your pump is already slowing down.
Using standard formulas and conversions, a pump engineer will test for variables such as the fluid’s temperature and viscosity and assess whether it is significantly impacting the pump’s performance. A professional will also advise you on what you can do to salvage the situation.
3. Cavitation
Cavitation occurs when bubbles accumulate around a pump’s impeller. The bubbles can form in any liquid in your pump, including water or oil. The bubbles then collapse, causing shock waves inside the flowing fluids and pump, and can destroy the impeller or the pump’s housing.
Installing the wrong pump is the most common cause of cavitation. When a pump operates at a lower pressure or higher temperature levels than it is designed to, cavitation can occur. To prevent this, always consult a professional to assess your needs and recommend the proper pump for the process you are running.
Use impellers made from high tensile materials in your pumping system. Always operate your pumps at the proper pressure and temperature.
A pump technician can verify that your pump is running at the right operating conditions and remedy a potentially problematic situation before the impeller is completely damaged.
4. Pump Curve Operating Below Normal
The pump curve is data comparing a pump’s ability to push liquids or produce flow against the maximum pressure it can deliver, also known as pump head. A pump operating below its standard curve should be a concern. The likely causes for a subpar pump curve operation are a blocked or damaged impeller, a blocked volute, or wear on the rings.
Preventative maintenance ensures that the pump always operates at its standard curve so that the velocity and flow are matching. During a maintenance routine, a technician measures the pump’s flow and the total head and compares these with the pump’s standard curve.
If the pump is operating below its curve, a well-versed technician can diagnose the root cause and recommend solutions to increase system flow and save you an unnecessary replacement.
Leakages, low flow, and other pump problems not only slow down the pump’s efficiency but can also damage other equipment. An experienced engineer will offer solutions to prevent further damage to your pumping system, increase its lifespan, and minimize your operational costs.
Pumps are a capital-intensive investment, and it is, therefore, paramount that you only work with trusted professionals. Contact Simonds Machinery Co. for an initial consultation, expert advice, and professional preventive maintenance, inspection, testing, and pump repair services.
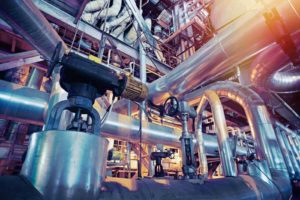