Avoid Breakdowns and Protect Your Investment: Tips for Industrial Pump Maintenance
When you’re responsible for overseeing an industrial process, it’s important that you stay aware of all possible threats to your workflow. Malfunctioning equipment can quickly become a serious problem that can cut into your profit margins and threaten your reputation with customers, so staying aware of warning signs and taking preventative actions is absolutely vital.
An industrial pump is likely to perform a task that no other individual piece of equipment can do. If your pump fails, then, it can leave you in the lurch as you struggle to find a solution that will get your process back on track.
It’s often been said that an ounce of prevention is worth a pound of cure, and when it comes to maintaining industrial pumps, that’s certainly true. Below, you’ll find some steps you should take to maintain your pumps and guarantee that you never find yourself in an unsustainable maintenance dilemma.
Temperature Control
Most industrial pumps operate under high pressure and involve the use of fluid components that may be vulnerable to increasing temperatures. Whether those increases are the result of excessive friction buildup or even a high ambient temperature in your facility, it’s important to monitor changes and act to keep them under control.
High temperatures can have many effects on an industrial pump, but the most serious is likely to be in its seals. As heat increases, moisture decreases, and vital rubber components degrade. This can threaten your closed system and may leave you vulnerable to a serious rupture.
Make sure that you keep your work floor at the lowest possible temperature that still allows you to control your energy costs and maximize employee comfort. Keep in mind that equipment functioning at high capacity will have a definite thermal effect, and be sure to factor that into your considerations.
Voltage Monitoring
Industrial pumps require a good amount of electricity to function at their highest efficiency, but that can represent a delicate balance. Excess energy may create an unstable situation that could risk a serious mechanical failure, or it may risk damaging electrical controls that govern pump operations and oversee your entire process.
Make sure that your industrial pumps are only plugged into outlets that provide the right amount of voltage as prescribed by the manufacturer. On an industrial floor running high-capacity machinery, it might be difficult to keep track of individual components. It’s important that you don’t allow yourself to be swamped by that difficulty.
Electrical surges may be difficult to detect since they typically affect the internal workings of your pumps. Since there may not be any obvious warning signs, it’s important that you continue to rely on preemption and avoid problems through careful planning.
Filter Cleaning
Sometimes, flow problems in your industrial pumps can be caused by old-fashioned dirt and grime. Most pumps have filtration systems that serve to purify water running through the system and remove any irritants and additives that may have infiltrated during the process. Keeping these filters clean and clear will help guarantee that you don’t deal with any sluggish operations.
In many cases, your pump will have a built-in observation window or valve that will allow for easy monitoring of your filter without stopping the pump and disassembling the apparatus. You should be sure to make checking your filter part of your regular oversight duties.
Simonds Machinery Company can provide the service and repair solutions you desire to keep your process running smoothly and efficiently. By following these suggestions, you can quickly diagnose problems and point the repair professionals to your exact spot of concern.
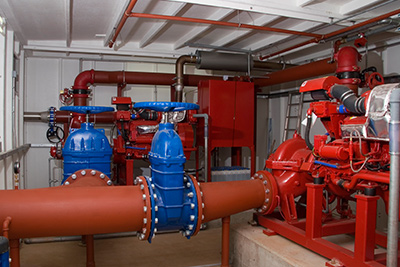