How Inefficient Pump Operation Lowers Performance and Drives Up Costs
Industrial pumps are used to move fluid for different applications and serve as the center of most industrial processes. Because these pieces are so common, plant managers may overlook them as an area to improve productivity.
The truth is, low pump productivity can lead to excess energy use and higher maintenance and repair costs. By maximizing system performance, you’ll reduce the overall costs associated with operating and maintaining your system.
Understanding Best Efficiency Point
The Best Efficiency Point, or BEP, is one of the key indicators of your pump’s performance. BEP refers to the flow rate where your pump operates most efficiently. In general, most pumps stray away from the flow point to some degree. However, you need to make sure that your pump only does so to a small degree.
Monitoring how close your pump is to the flow point is one of the best places to start when monitoring the performance and efficiency of your pump. By monitoring the BEP, you can make adjustments and ensure that your pump operates at the most efficient flow rate to maximize performance and reduce maintenance and repair costs.
If you’re operating too far off BEP you’re not using your pump as efficiently as possible. Operating a pump too far off the BEP over an extended period also causes excessive wear and tear on your system that could lead to pump failure.
Cavitation
Operating the pump too far right of the BEP increases the risk of cavitation, which occurs when bubbles in the liquid burst with force.
Cavitation damages the pump housing and over time can cause your pump to fail because operating your pump too far off BEP causes an imbalance in the forces inside of your system, which wears down your system.
Think of the flow rate of the fluid in your system. If the flow rate is inefficient and vapor bubbles form and violently collapse, the housing inside the pump will clearly take a beating. Now, imagine that your pump is taking that beating continuously over the course of a year and you can see how cavitation causes excess wear and tear on your system that leads to increased maintenance and repair costs.
Excess Vibration
Vibration is another repercussion of operating your pump too far off the BEP, resulting in areas of the shaft that bend, causing poor pump performance. The hydraulic imbalances caused by operating too far off the BEP can cause problems within the impeller when the liquid vaporizes.
The excess vibration can cause liquid to implode with high force, which then sends socks waves throughout the system. Over time, operating consistently in this manner leads to impeller damage, system corrosion and may ultimately cause your pump to fail.
Flow Recirculation
When you operate your pump close to the BEP the fluid inside flows in the much more uniform manner. The further you get away from the BEP, the pressure becomes distorted and your system suffers. When you operate too far off the BEP, the pressure gradient can cause localized flow reversal, a phenomenon known as flow recirculation.
Recirculation can occur at the suction of the impeller, the discharge, or both. The phenomenon of recirculation causes significant instability and reduces the flow rate, which not only puts stress on your system but also leads to pump failure if portions of the impeller break off. When portions of the impeller break off, repair costs are significant.
As the lifeblood of your operation, efficient pump operation should be a top priority. Simonds Machinery Company offers pump maintenance, repair, inspection and testing to maximize your systems performance and overall productivity. Call us today to find out how we can help with your business needs.
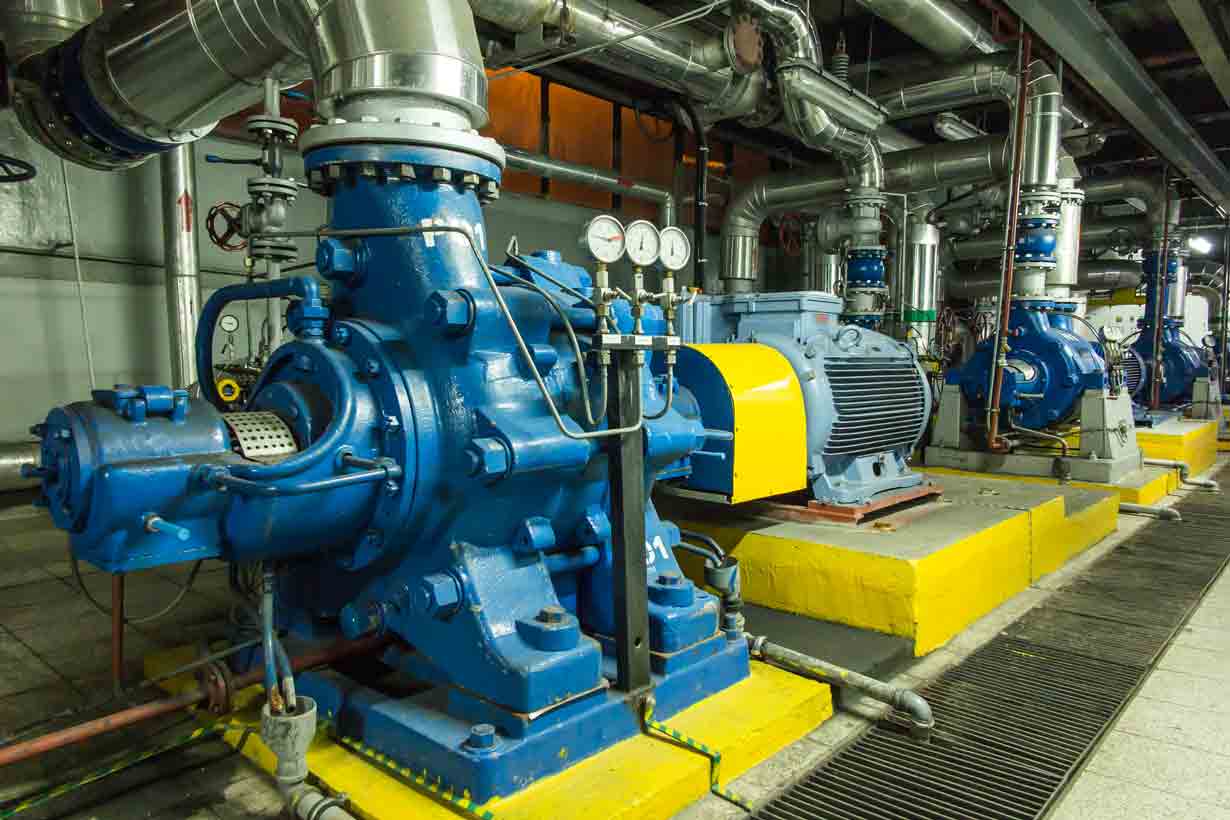